Metal Injection Molding (MIM)
What is MIM?
Metal injection molding (MIM) is a manufacturing process that combines the principles of plastic injection molding and powdered metallurgy to shape metals such as Stainless steel, Nickel Iron, Copper, Titanium, and more. This process allows designers to have greater freedom and flexibility in their design, resulting in more opportunities for innovation.
Here is a closer look at the steps involved in the MIM process:
- Mixing and granulating: The metal powder is mixed with a polymer binder to create a feedstock material.
- Molding: The feedstock material is injected into a mold to create the desired shape.
- Binder removal: The molded parts are then heated to remove the binder material, leaving behind the metal particles.
- Sintering: The parts are sintered, or heated to just below their melting point, to fuse the metal particles together and create a solid, finished product.
MIM is an advanced and supplementary technology in metal parts manufacturing. Unlike traditional technology when producing small size, complex shapes metal components in large quantities, MIM advantages have been maximized, so many small and complex metal parts we used today have a great chance made by MIM.
1. Steady quality, high efficiency, and economical manufacture
of high-volume complex parts.
2. High utilization rate of raw materials. Material properties are equivalent to wrought alloys.
3. The direct manufacture of small size metal parts (up to 500 gm) with complicated geometric shapes.
4.High precision, one - time molding.
Materials For MIM
Low Alloy Steels, Stainless Steels, Titanium, Heavy Alloy
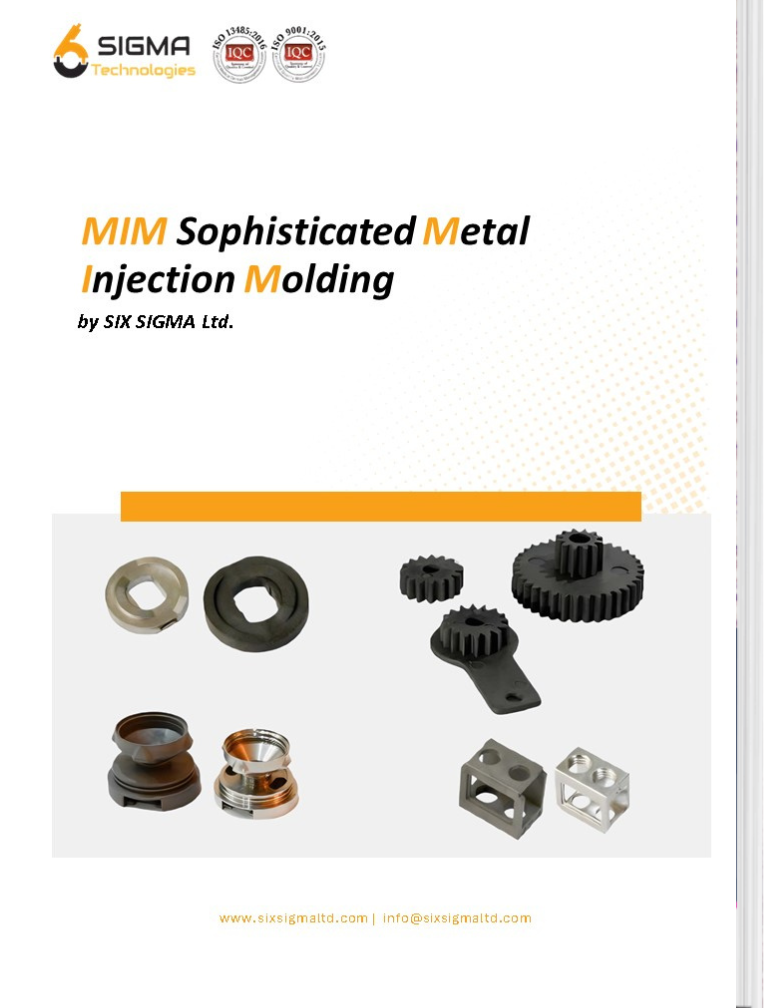
Metal Injection Molding: A Newly Designed Guide
Explore our guide on Metal Injection Molding, an advanced manufacturing process revolutionizing the production of small, intricate components with unparalleled precision and cost-effectiveness. Discover the benefits, applications, and design insights in this brochure
Customized Production Tooling
At Six Sigma, we offer unique tooling solutions for customers with low volume requirements. We can make mold for most plastic and metal product. Customized packaging and surface treatments are available.
Our skilled engineers, skilled workforce, and state-of-the-art machinery enable us to deliver low-volume and high-quality tooling solutions.
From A CAD File to the Finished Part
We are proud to accompany your project all the way from concept, design, and production and delivery. The Computer-Aided Design (CAD) software, including UG and Pro-e, helps us (to) optimize your design.
Our experienced toolmakers and state-of-the-art machinery enable us to accommodate low-volume as well as high-volume production. The completely in-house service expedites your plan to the market with the minimal amount of time and money.
Design for Manufacturability (DFM)
We welcome the early involvement of our customers in part and mold design using Design for Manufacturability (DFM) Review which is the key to successful part and product development.
At Six Sigma, we emphasize the benefits of DFM to our clients with the knowledge that this powerful diagnostic tool will anticipate problems, find solutions, and reduce risks, create a more efficient production cycle.
Your molds are made with high-quality P20, Nak80, 738H, H13, S136 steels. We use multi-axis CNC mills, grinders, and EDM machines to create complex geometries with multiple surface finishes, from the highest optical polishes to matte and everything in between.